Sommario
Manutenzione Industria 4.0: l’Analisi delle Vibrazioni prolunga la vita delle Macchine
I Vantaggi della Manutenzione 4.0 Predittiva basata sull’analisi delle vibrazioni
Come Funziona la Manutenzione Predittiva basata sull’analisi delle vibrazioni
- Architettura Hardware e di Sistema
1.1. Sensori di Vibrazione
1.2 Infrastruttura di Comunicazione
1.3 Gateway e Software
1.4 Integrazione e comunicazione dati - Raccolta dei Dati
- Apprendimento Basato sul Machine Learning
- Rilevamento e previsione di anomalie
- Dashboard di Monitoraggio
- Installazione
Manutenzione Industria 4.0: l’Analisi delle Vibrazioni prolunga la Vita delle Macchine
Nell'Industria 4.0, l’automazione industriale sfrutta diverse tecnologie con l'obiettivo di migliorare il lavoro e aumentare la produttività.
La manutenzione nell’Industria 4.0 ha un ruolo centrale nella prevenzione ed è capace di rispondere alle necessità di prolungamento della vita utile residua dei macchinari (RUL). Questo è possibile tramite la manutenzione predittiva, innovazione rivoluzionaria che ha saputo trasformare le modalità di mantenimento e ottimizzazione delle prestazioni dei motori elettrici.
Il sofisticato algoritmo utilizzato analizza le vibrazioni, rendendo possibile la prevenzione di guasti al motore elettrico. Questo consente di ridurre significativamente i tempi di fermo macchina, che diventano pianificabili.
Vediamo in questo articolo tecnico le caratteristiche della sofisticata tecnologia di machine learning e come questa può portare vantaggi nella gestione e manutenzione delle macchine.
I Vantaggi della Manutenzione Predittiva basata sull’analisi delle vibrazioni
Nell’Industria 4.0, la manutenzione predittiva sfrutta la tecnologia di analisi delle vibrazioni per permettere una migliore gestione delle risorse e un risparmio di costi.
I principali vantaggi di un sistema di manutenzione 4.0 sono:
- Riduzione dei tempi di fermo macchina: la rilevazione precoce di potenziali problemi permette di pianificare la manutenzione e scongiurare guasti imprevisti;
- Efficienza dei costi: la prevenzione riduce la necessità di riparazioni o sostituzioni di emergenza, che tendono ad essere molto costose;
- Durata prolungata del motore: il monitoraggio continuo e l'intervento tempestivo allungano la vita operativa del motore;
- Decisioni basate sui dati: ottenere informazioni in tempo reale rende possibile una migliore pianificazione della manutenzione e un'allocazione delle risorse più efficiente;
- Integrazione flessibile: il supporto del sistema per i protocolli OPC UA e MQTT consente una perfetta integrazione con altri dispositivi e sistemi industriali.
Come Funziona la Manutenzione Predittiva basata sull’analisi delle vibrazioni
Questa tecnologia di manutenzione 4.0 utilizza l’intelligenza artificiale, strumento cruciale per analizzare i dati e proporre un intervento di prevenzione dei guasti.
La manutenzione predittiva è una delle app di NOA, la nuova architettura di KEB aperta e basata su microservizi: i motori diventano smart grazie ai sensori e ad una tecnologia avanzata, che ne rilevano le anomalie in tempo reale e inviano i dati al software di KEB basato sull'IA, che li analizza e li elabora. I sofisticati algoritmi di KEB basati sul machine learning elaborano previsioni per evitare i fermi macchina.
La strategia di manutenzione predittiva si basa su sensori, wireless o cablati, che monitorano le vibrazioni del motore sugli assi X, Y e Z. In questo modo, viene garantita un’analisi completa dello stato e della salute del motore.
Vuoi approfondire la nostra soluzione di Manutenzione Predittiva?
1. Architettura Hardware e di Sistema
Quali sono le specifiche di questo sistema di manutenzione 4.0? Scopriamo insieme l’architettura hardware e di sistema.
1.1 Sensori di Vibrazione
Il sistema di manutenzione predittiva si basa sull’analisi delle vibrazioni, tramite sensori di vibrazione che possono essere wireless o cablati. Questi sono montati in punti strategici del corpo del motore, per acquisire dati in tempo reale su più assi.
In particolare, la funzionalità wireless garantisce flessibilità nell’implementazione. Invece, il collegamento cablato garantisce un’alimentazione affidabile minimizzando le esigenze di manutenzione e garantendo un funzionamento continuo. I sensori vengono alimentati a batteria, dalla durata di 2 anni, oppure tramite cavo coassiale DC 9-36V e hanno una frequenza di campionamento fino ad un massimo di 25.6Khz su 3 assi, X, Y e Z.
La comunicazione con il gateway avviene tramite Bluetooth a basso consumo energetico (BLE 5.0).
I sensori funzionano in condizioni ambientali tra i -40°C e gli 85°C. Hanno un grado di protezione IP67, secondo lo standard IP, ed Ex ia IIC T4 Ga, secondo la direttiva ATEX dell’Unione Europea.
1.2 Infrastruttura di Comunicazione
I dati sulle vibrazioni rilevati dai sensori vengono trasmessi via Bluetooth ad un ricevitore centrale: il dispositivo di rete gateway funziona come hub del sistema, elaborando e gestendo i dati in entrata.
Questa infrastruttura di comunicazione basata su Bluetooth garantisce un trasferimento dei dati efficiente, sicuro e a basso consumo energetico nell’ambiente locale.
1.3 Gateway e Software
Il gateway è dotato dei software necessari per analizzare i dati delle vibrazioni. Il software include algoritmi di apprendimento automatico che rilevano anomalie e fanno una stima della vita utile residua (RUL).
Il gateway offre due modalità primarie di visualizzazione dei dati: locale e remota. In locale, i team di manutenzione possono accedere a grafici e dashboard in tempo reale che forniscono informazioni immediate sullo stato del motore. Inoltre, il gateway può inviare dati al cloud per il monitoraggio remoto, l'archiviazione a lungo termine e analisi più sofisticate.
Il gateway viene alimentato tramite trasformatore di potenza 9-18 Vdc o 230 Vac con adattatore e funziona con interfaccia di rete Ethernet, Wi-Fi o rete cellulare. Possiede 4 GB di memoria, 120 GB di storage e può essere collegato ad un massimo di 4 sensori.
1.4 Integrazione e comunicazione dati
Per permettere una più ampia integrazione del sistema, il gateway supporta i protocolli di comunicazione MQTT, TCP/IP, UDP e OPC UA. Questa flessibilità permette la comunicazione dei dati con altri dispositivi e sistemi, consentendo una perfetta integrazione nei framework IoT esistenti e nei sistemi SCADA.
2. Raccolta dei Dati
La raccolta dei dati è lo step di partenza del processo di analisi delle vibrazioni. e dura circa un mese. In questo periodo i sensori raccolgono continuamente dati, creando una linea di base dettagliata. Questa rappresenta le normali condizioni operative del motore e tiene conto delle tipiche variazioni e delle condizioni di carico: sarà il punto di riferimento per poi evidenziare eventuali anomalie.
3. Modello di apprendimento Basato sul Machine Learning
La linea di base ottenuta viene utilizzata per addestrare il modello di apprendimento automatico nel gateway. L’apprendimento si basa su machine learning: l’algoritmo impara i normali modelli di vibrazione del motore e sa distinguere il rumore standard di funzionamento da potenziali problemi meccanici. Il modello di apprendimento è altamente sensibile: riesce a rilevare anche lievi deviazioni dalla base stabilita.
4. Rilevamento e previsione di anomalie
Dopo l’addestramento, il sistema diventa operativo tramite il rilevamento dei dati, permettendo la previsione di anomalie.
Il gateway monitora continuamente i dati delle vibrazioni e li confronta con il modello di riferimento. Le anomalie possono presentarsi ad esempio come frequenze di vibrazione, ampiezze o modelli insoliti. Se queste vengono rilevate, il sistema le segnala come potenziali indicatori di problemi meccanici quali usura dei cuscinetti, disallineamento o squilibrio del motore.
Inoltre, il sistema fornisce informazioni predittive sulla vita residua del motore. Analizzando le tendenze dei dati sulle vibrazioni, il sistema valuta per quanto tempo il motore può ancora funzionare prima che si verifichi un guasto, prevedendo potenziali anomalie. In questo modo, si possono pianificare riparazioni e sostituzioni nei momenti migliori, riducendo le interruzioni, con l’obiettivo di prolungare la vita del motore.
5. Dashboard di Monitoraggio
Per la fase di monitoraggio, il sistema offre due opzioni di visualizzazione dei dati, entrambe basate sul software Grafana:
- in locale gli utenti possono visualizzare grafici e dashboard sulle vibrazioni e le prestazioni dei motori in tempo reale, direttamente sul posto, per ottenere informazioni immediate, con l’obiettivo di prendere decisioni rapide per risolvere i problemi;
- da remoto, si ha un accesso più ampio, maggiore flessibilità, archiviazione a lungo termine e analisi più sofisticate. Con questa soluzione, basata sulla piattaforma cloud di KEB, diventano possibili monitoraggio e diagnostica remoti, garantendo sorveglianza continua dei macchinari anche se questi si trovano in diverse sedi.
Entrambe le dashboard di monitoraggio si possono personalizzare per allineare i dati presentati alle proprie necessità operative specifiche.
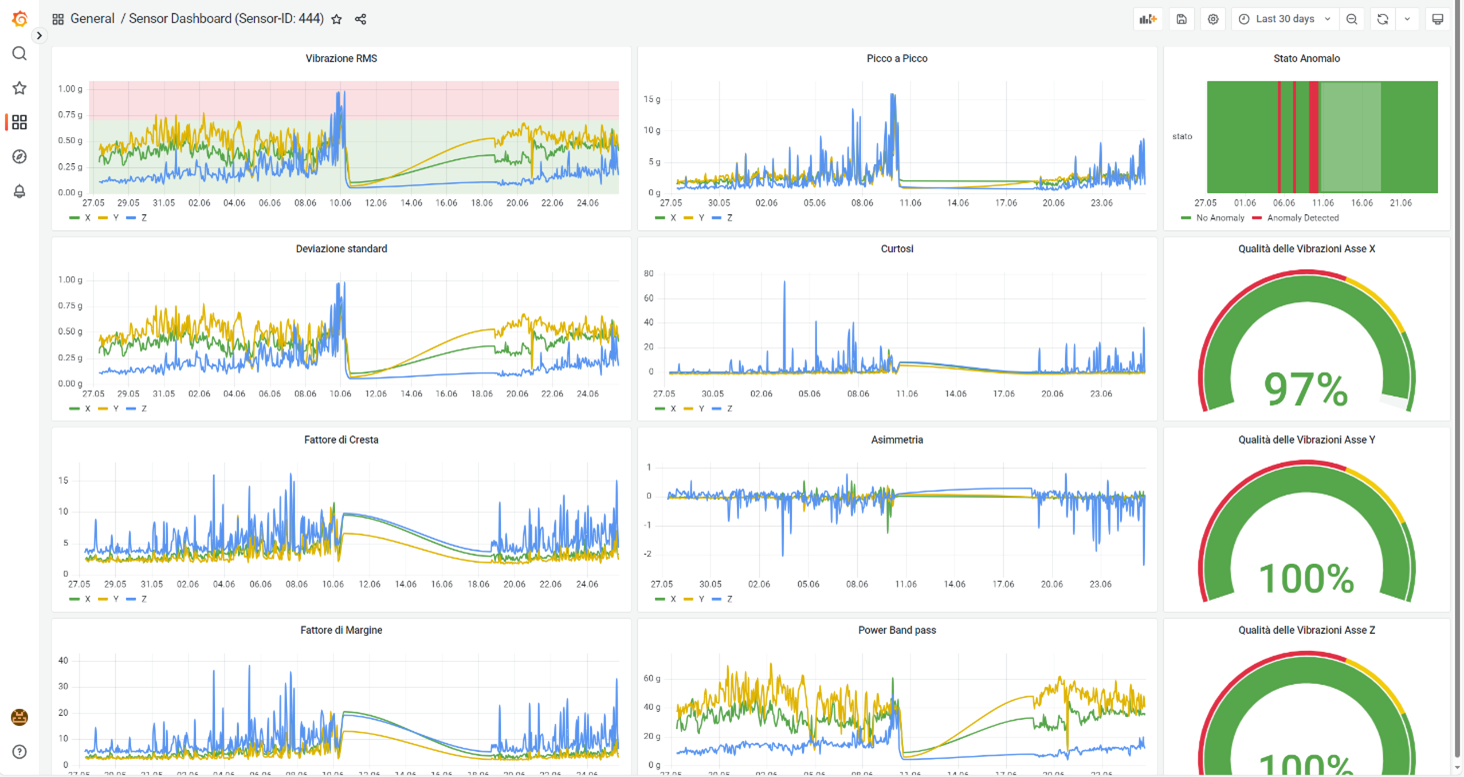
6. Installazione
L'installazione dei sensori di vibrazione può avvenire scegliendo la modalità migliore per le proprie esigenze, a seconda dell’applicazione e delle preferenze di montaggio.
Sono possibili le seguenti opzioni di montaggio:
- Montaggio con resina epossidica: il sensore viene fissato direttamente sul motore tramite adesivo a resina epossidica, che garantisce una forte adesione e di conseguenza una trasmissione ottimale delle vibrazioni.
- Montaggio a vite M6: si utilizza una vite M6 per fissare il sensore in modo stabile e permanente;
- Supporto a perno M8-M6: il sensore viene fissato tramite un supporto a perno filettato M8-M6, per offrire elevata stabilità e facile rimozione quando necessario.
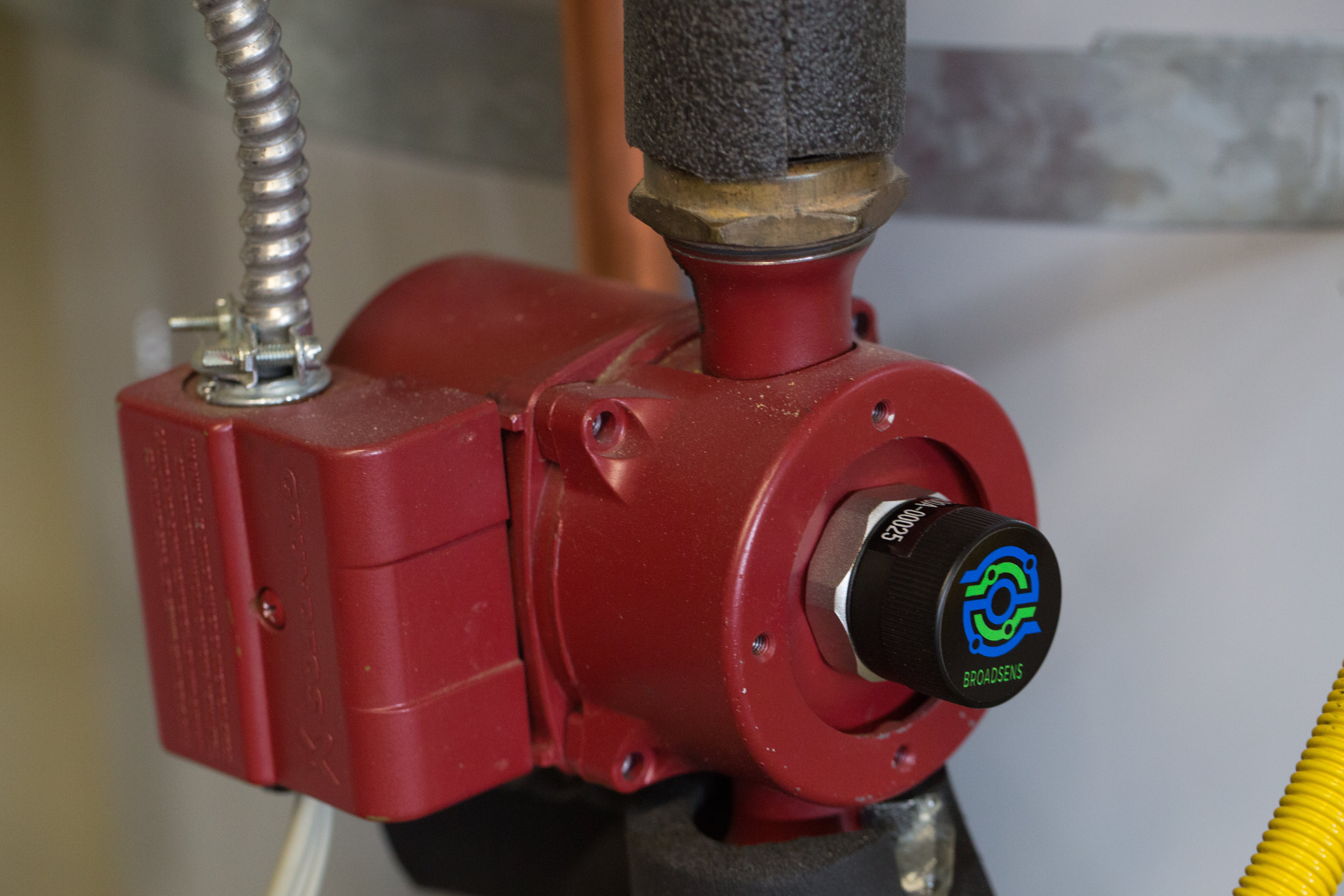
Integrando l’analisi delle vibrazioni con un'architettura hardware e di comunicazione robusta, è possibile garantire un funzionamento affidabile ed efficiente dei motori elettrici. Questo approccio globale alla manutenzione e alla gestione delle macchine, permette di migliorare la longevità dei motori, oltre ad ottimizzare le prestazioni operative complessive del sistema.Vuoi saperne di più sulla manutenzione nell’Industria 4.0?
Vuoi saperne di più sulla manutenzione nell’Industria 4.0?
Oppure contattaci al seguente indirizzo email dedicato: noa@keb.it
Mehdi Rahmanian risponderà direttamente alle tue richieste